Why subcontract management is a cornerstone of project risk management
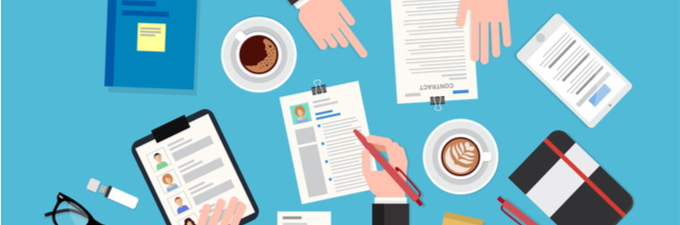
To manage a project effectively, project risk management is vital. The changing world faces new challenges including climate change, artificial intelligence and technology, and more. We have explored three cornerstones of project risk management in my previous blogs, and this final blog focuses on subcontract management, the fourth knowledge cornerstone.
Many companies outsource 60 to 70 per cent of their contract scope to subcontractors because they do not have an in-house capability to provide the service or product. Other reasons may be that the subcontractor can provide services at lower costs or provide technology the company doesn’t have. This trend is expected to continue and in fact increase for future work because of skilled labour shortages and companies are increasingly foregoing full-time employees as part of the changing workforce trend that is underway. The selection and management of qualified subcontractors is paramount to avoid costly schedule delays and cost overruns. In other words, risks to your project.
Here are various subcontractor risks that can occur during your project and ways to solve them:
Subcontractor proposal risk
Subcontractors have insufficient time to generate a complete and thorough proposal. Typically, the response time and process of a customer’s request for proposal is sixty days. This means your subcontractor has three to four weeks to prepare and submit their proposal. There is very little time for the subcontractor to solicit bids from their major suppliers and generate their own cost and schedule data for their proposal. As a result, the subcontractor’s proposal may not be solid (includes some soft cost and schedule areas). The risk mitigation plan is to add margin to their proposal before inserting it into your proposal. This can help cover the increased cost and schedule you anticipate when you go back with updated documents for a best and final proposal after contract award.
Subcontractor execution risk
The risk here is the subcontractor may not manage their cost and budget to the contract. What is the mitigation plan? It involves selecting the best qualified subcontractor and managing them frequently and carefully. After receiving the subcontractor’s proposals, select a team to review each proposal and compile a list of questions designed to understand the basis of the proposals. This process is fact finding. The questions are submitted to subcontractors with a request to provide answers quickly (within two or three days). Once the responses are in, fact finding meetings are arranged with the subcontractors. An onsite visit is preferred if the subcontractor scope is large and complex. After the fact finding is complete, an SRA (supplier rating assessment) is conducted to help select the winning subcontractor.
Below is an example of an SRA form, an Excel file tailored for the specific subcontract and project. The team decides the topics and their weight; the idea is to select the major topics that may impact the success or failure of the subcontract. Ratings are made by the team based on consensus by all members for example in the table below, the ratings are given from one to five, five being the best possible score. The overall highest score determines which company would be recommended.
Subcontract major suppliers
The risk here is that a major supplier of your subcontractor does not execute well causing substantial impact to their contract with you which in turns causes significant impact to the project. Usually, the subcontractor is evaluated closely but not their suppliers. During fact finding, evaluate the subcontractor’s suppliers as much as possible. I have seen this risk realised a number of times;it is a real risk to consider.
Ensure the subcontractor submits a monthly report with a cost and schedule status, risk management status, problems, and other status information. If you feel everything is going well, then an onsite visit may only be required quarterly. However, if it looks there are issues or you haven’t worked with this subcontractor before, visit monthly or maybe more often until you’re comfortable. If things go really badly, invite them to your facility to meet with the programme manager. This approach usually gets their attention and they commit to improving.
Subcontractor risk example
My company, a large defence contractor, selected a small subcontractor to manufacture, assemble, and test tactical communications vehicles for us. It was a firm fixed contract to include delivery of a first article unit and several production options.
The problem was we overwhelmed them with frequent visits involving six or seven engineers and managers from our company. Each time we visited, virtually every member of their team stopped work to support our visit. It became clear after a few months that they had no experience working with a large company. As a result, they incurred a substantial schedule delay and had to absorb a large cost penalty to complete the first article unit. They refused to execute the production options. Eventually, we renegotiated the option prices and they completed the contract.
Conclusion
Subcontractors risks can cause more harm to a project than known and unknown risks (discussed in earlier blogs). It is important to understand how to select and manage subcontracts to minimise subcontractor risks to your project. Without understanding project management, earned value management, risks and subcontract management, it is difficult to achieve effective project risk management. Master the cornerstones and the challenges of the future, the new risks and opportunities will become easier to manage.
You may also be interested in:
- The key to successful project risk management
- Making risk work for your project in APM Learning (🔒)
- How EVM is a cornerstone of project risk management
- Understanding and managing risks is a cornerstone of project risk management
Image: Biscotto Design/Shutterstock.com
0 comments
Log in to post a comment, or create an account if you don't have one already.