How to turn around a safety culture, according to one APM Award winner
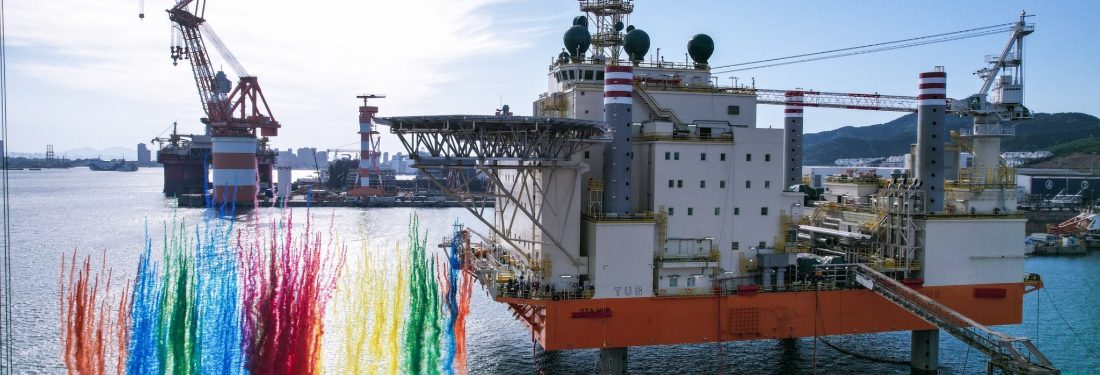
What’s the secret of great safety performance? It isn’t about working up a slick safety slogan or just making sure all your procedures are up-to-date. The uncomfortable part of managing safety is that it comes down to people and the choices they make. On a heavy industry construction project, that can mean tens of thousands of individuals having to do the right thing every second of every day, even when no one is looking.
The good news is that it is possible to create an environment where people genuinely care about each other and believe in the importance of working safely – to the extent that, in any situation, the likelihood of the correct decision being made outweighs the opposite. In this kind of environment, even if someone does make a mistake, the outcome will be far less severe, because gaps will have been anticipated and robust protection measures put in place in advance.
As project leaders, we are responsible for building and nurturing this environment, which is the biggest factor influencing success. Below, I share some ingredients that made a real difference in creating an inclusive and collaborative culture of care on the Greater Tortue Ahmeyim Quarters and Utilities (GTA QU) Platform project.
Leadership alignment on common goals and holding each other to account
The GTA QU project leadership team invested time identifying the factors that would define our safety success, including our safety goals and how we would behave and work together to achieve them. We captured these in a project safety charter. Our goal was Zero Harm to people, which is an absolute, an extremely challenging bar to meet. This was not a safety department responsibility, but one that we all collectively and individually adopted.
We kept the signed safety charter on the wall and frequently referred to it to help guide our decisions, challenging each other to fulfil the commitments. We were looking out for each other and upholding our shared values. One-on-one coaching was occasionally required to adjust behaviours to allow us all to show up consistently and visibly as a combined leadership team in front of the wider workforce. This was always done in the spirit of teammates building on each other’s strengths to grow and be the best that we could be.
Consistent and visible leadership: walking the walk
We worked hard as a project team to stick to our values and demonstrate them consistently over a three-year period, even when times got tough. We established a systematic programme of oversight and verification activities that allowed the team to ensure that what we thought should happen at the workface really was happening through observation and conversation with those on the front line. Senior leadership participated in the regular safety walkdowns and held conversations with those actually performing the work.
Early in the construction phase, I was concerned that some of our KPIs were trending downwards and safety observations were picking up negative behaviours and unsafe conditions. Despite schedule pressures, we stopped project activity on site for a day to dedicate our time to improving safety. This was a public demonstration of leadership commitment to upholding safety standards, but everyone working on our project also had the individual authority to stop any unsafe activity. Many team members initiated time-outs for safety when an unsafe act or condition was observed, allowing work to resume once safety concerns had been addressed.
At times, tough decisions were needed. In one instance, a subcontractor failed to respond to concerns over repeated violations of site safety rules. In agreement with the contractor, this subcontractor was removed from the project. All of this was done under a ‘just culture’ framework to ensure actions were not retaliatory in nature and individuals were not punished for management system failings.
Innovate and evolve, refresh and upskill
Safety can be a dry subject. So how can we keep people engaged? Our solution was to make sure there was something in it for everyone, both short term (rewards and recognition) and long term (training and upskilling). That, plus ensuring the message was always relevant to the hazards and risks of the work at hand. What was relevant for structural steel fabrication at the start was not sufficient for multi-trade construction or system energisation during commissioning. We held multi-disciplinary readiness reviews prior to each major change in activity or risk profile on site, and also evolved our safety programme.
As we moved into multi-trade construction, we launched the Zero Harm programme, which focused on workforce and supervisor safety training, hazard awareness and positive reinforcement for good safety behaviours. Posters and banners were put up, and guidance booklets, safety awards and gifts for safety excellence were given at programme launch events and weekly mass toolbox talks.
As we prepared for the commissioning phase, we launched the Finish Safe, Finish Strong campaign. This had worked well on previous projects, training, upskilling and preparing the workforce for the additional hazards of stored energy and electrical energisation associated with commissioning.
At each campaign launch, we reminded everyone of the project safety charter commitments, and all project members re-signed a giant banner with the charter written on it. We also marked significant safety milestones with gifts for the entire project workforce.
Build ownership
Building ownership of the safety outcome within the delivery line was a challenge, but the progress we made here was the biggest factor that influenced safety performance. The theory goes: instead of a handful of people acting as ‘police’ to catch violations, the entire workforce begins to self-police and proactively manage issues before they arise. This improves safety and also positively impacts the quality and productivity of work.
Turning theory into practice was a hard journey, but we made enormous progress. One innovation introduced by the contractor stands out for its simplicity and effectiveness. Those caught violating safety rules, together with their supervisor, would present the incident as a safety learning at the next mass toolbox talk to the entire project. Not in a humiliating or punitive way, but as a genuine presentation of learnings, what went wrong and what could be better.
One supervisor who had been reluctant to follow safety rules became a passionate and vocal safety champion after delivering his safety moment to the project – which probably had a far more lasting impact on safety on our project than any speech by a senior manager!
You may also be interested in:
0 comments
Log in to post a comment, or create an account if you don't have one already.